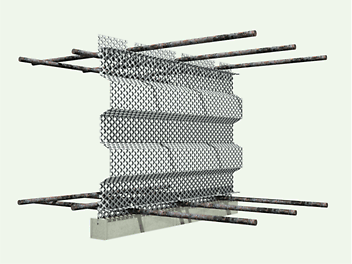
Improving on-site efficiency
Permanent stop-end systems like BECOSTOP provide full continuity of reinforcement for the installation of construction joints and overcome the issues most associated with temporary timber shoring, starting with the inherent delays.
Consecutive bays can be poured on consecutive days with BECOSTOP, which could deliver a four or five-day advantage when casting deep reinforced slabs for large infrastructure projects. With traditional systems, the stop-end would need to be built elsewhere on site, potentially even off site depending on the space available.
BECOSTOP comes to site ready to install, with a full temporary works design provided, including structural design and CAT checks. This is in stark contrast to the absence of calculations behind timber shoring for a similar application.
Strength and consistency of the construction joints created are key benefits of using BECOSTOP when laying a slab in multiple smaller pours. The continuity of reinforcement offered by BECOSTOP also ensures the diameter of the reinforcement steel will not have to be increased.
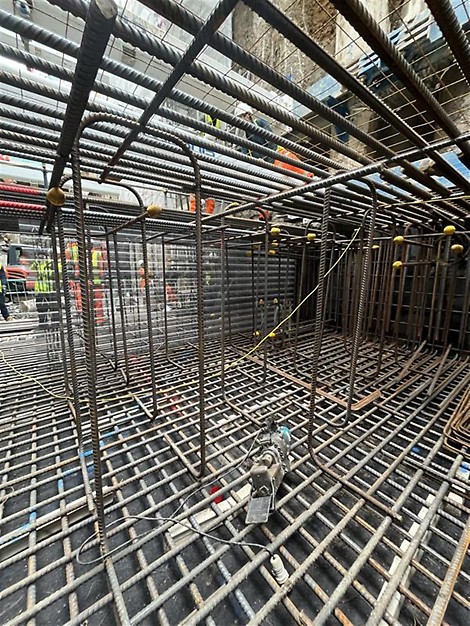
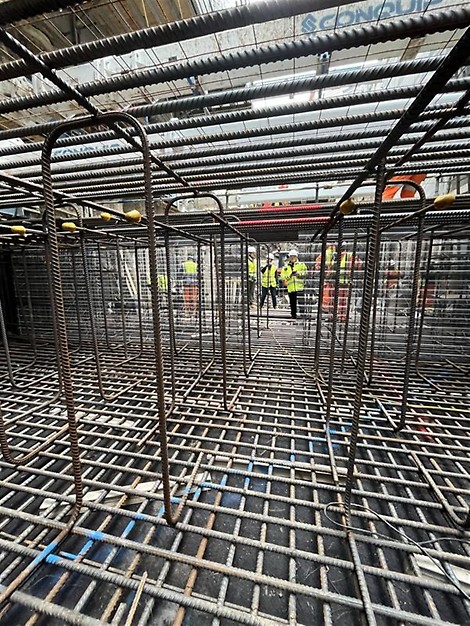
Traditional shuttering with smooth timber risks leaving a day joint with a low-bearing capacity, unless the surface of the joint is scabbled to roughen it or is chemically treated prior to the next pour - all of which requires additional time, labour and cost.
The quality of the joint now depends on the experience of the team undertaking the scabbling process, which also faces the risk of vibration white finger. There are also the noise and silica containing dust considerations of this slow process, which not only affects workers involved or in close proximity, but neighbours to the site.
The problems extend beyond their low-bearing capacity, with poor joints also compromising the structural integrity of the concrete. Joints formed without remedial work to create a strong bond, reduce the slab’s durability and increase the risk of water ingress, which can lead to the corrosion of the reinforcement steel.
A key profile solution
The BECOSTOP panels are manufactured using steel from a sustainable source and utilise a unique trapezoidal profile which allows for full 100% bearing capacity according to EC2. The perforations are designed to reduce the flow of concrete through them, which allows enough time for it to cure and create the key profile needed for strong construction joints. The profile of the perforations in the panels also allows for a release in concrete pressure, which means we can design at 50% of full hydrostatic pressure for the pour.
The BECOSTOP panels are designed to create a joint surface with a roughness coefficient [c] of 0.5, which exceeds that of a traditional joint created with timber and scabbling when the coefficient is typically 0.2.
The elements allow for a limited flow of concrete, which significantly reduces the pressure on these stop-end units and requires a lower concrete pour pressure, which in some cases can be reduced by 50%. There is also the added advantage of these key-profiled joints eliminating the need to install couplers into the structure by providing full continuity of reinforcement.
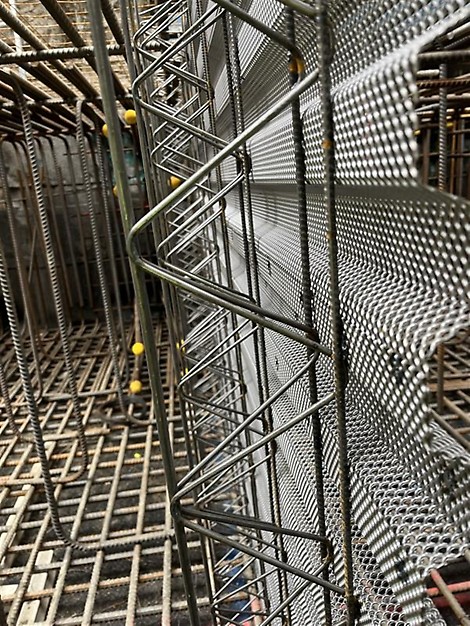
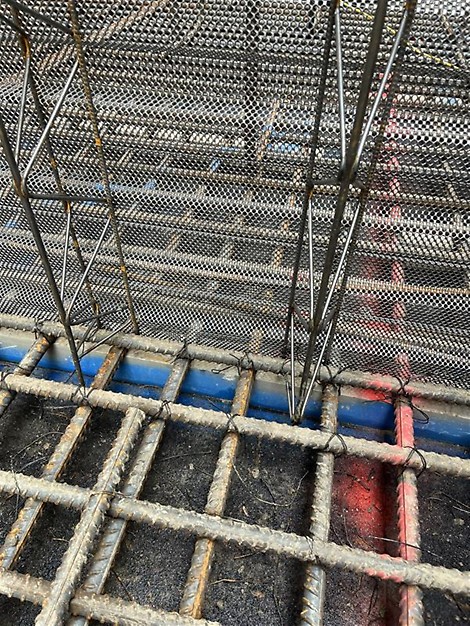
Rather than needing skilled carpenters to create the timber shuttering, the BECOSTOP panels are fixed to the rebar cage using inexpensive tying wire and the skills of site labourers, with no extra supports needed for the panels, which self-support up to 1.5m.
At PERI, we can provide full technical and design support, with drawings and temporary works calculations provided for any project to ensure each concrete slab can be created more quickly.
BECOSTOP is the modern solution for projects that require day joints or have wall stop ends. The panels are manufactured to order and tailored to the unique design requirements of each project, ensuring they are ready to install directly from the pallet.
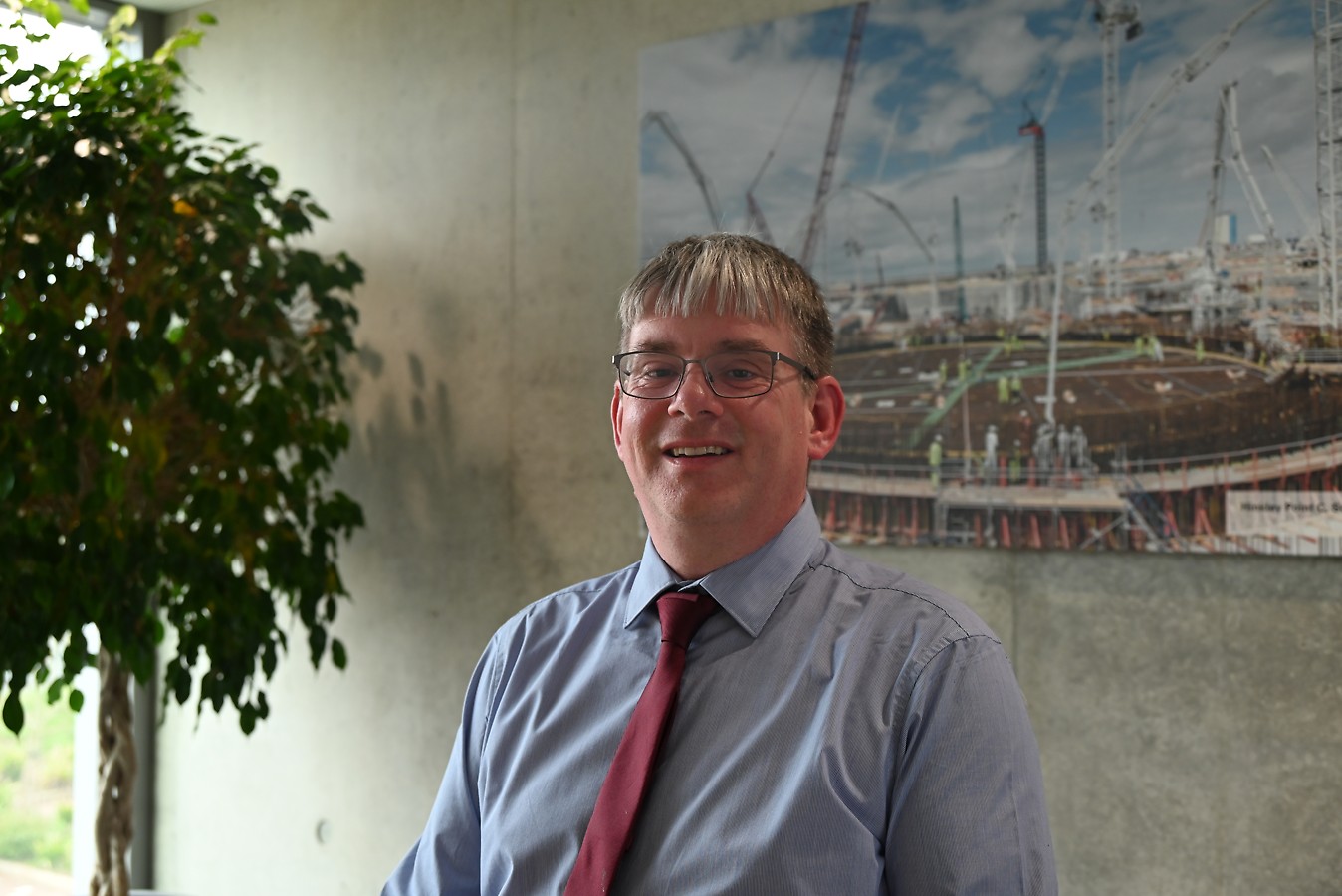
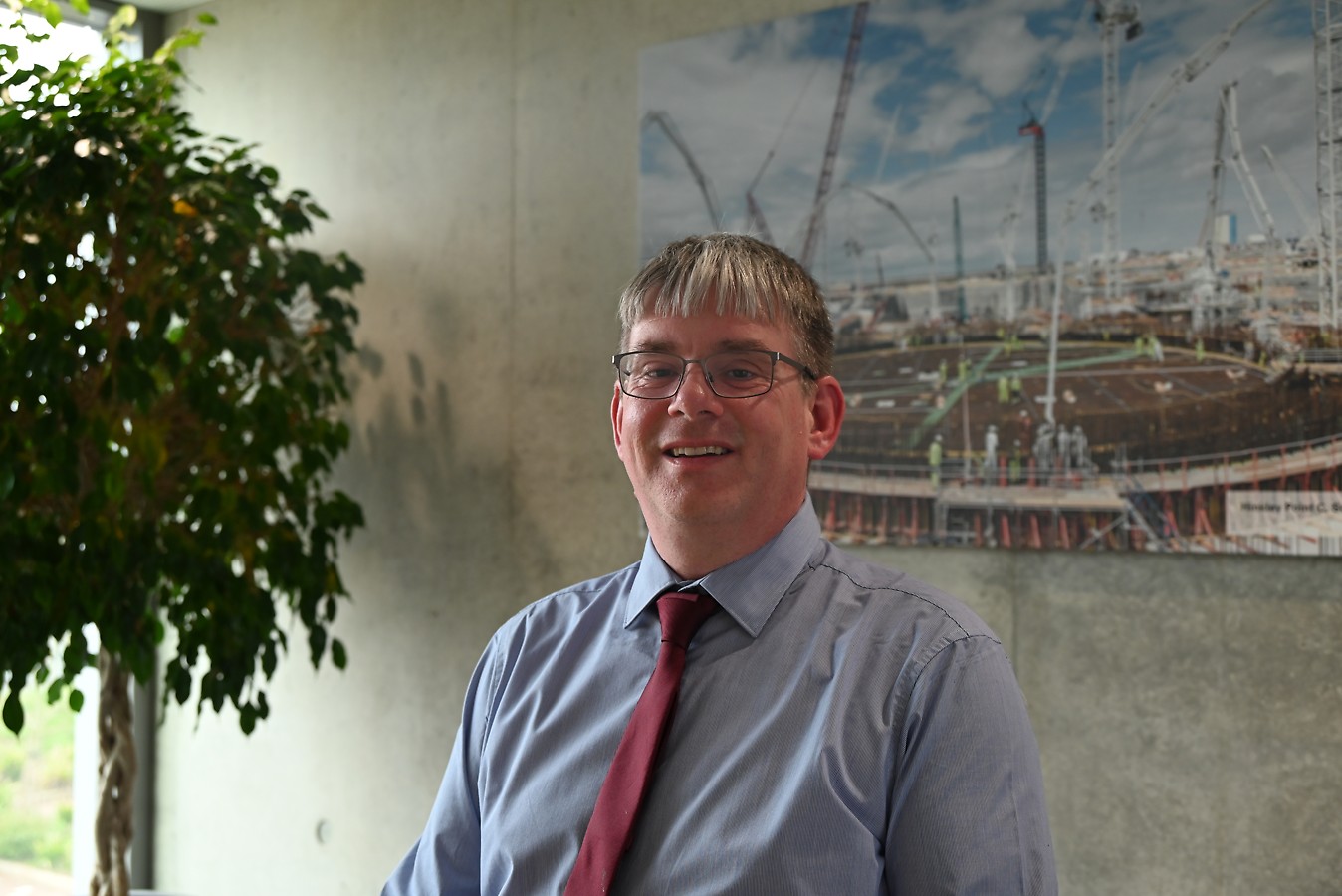
The BECOSTOP system allows contractors to make up time on site, save the cost of the timber and carpenters needed to fit it, whilst delivering a result with the attributes of a monolithic slab, rather than one with inherently weaker construction joints.