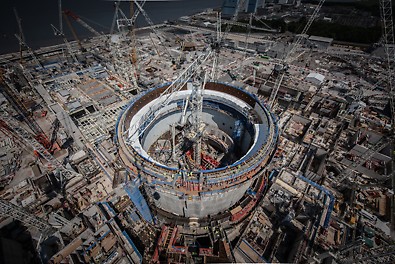
Why is early engagement key?
Very rarely are the proposals or construction requirements for these projects ever simple. They often require a lot of skilled engineering due to the level of complexity.
It’s important for preconstruction and methods teams to bring temporary works specialists into the conversation early. Engaging with the project team during the pre-design stage presents an opportunity for our team to help improve the buildability of a project and reduce costs.
In contrast, a more traditional engagement model limits the ability to make changes collaboratively, making it more difficult and expensive to implement alterations later on.
Value engineering
As the cost of raw materials remains high, value engineering is becoming a fundamental part of procurement and efficiency in the infrastructure segment.
Maximising material utilisation and application is key. For example, our PERI UP scaffolding has been used across infrastructure projects like the A465 Heads of the Valleys scheme and HPC to install and restrain reinforcement whilst giving full access to operatives for concrete pours. The same system can be used throughout the construction sequence with minimal adaptions required.
Again, engaging early on in the process plays a crucial role in value engineering and maximises the benefits for contractors. It enables our sales team and design engineers to collaborate with sub-contractors and main contractors to identify the complete requirements and explore how products can be reused or recycled for multiple purposes.
Rather than focusing on individual product applications, this approach optimises the functionality of the entire solution, while keeping costs low throughout the project lifecycle to achieve the best value for money.
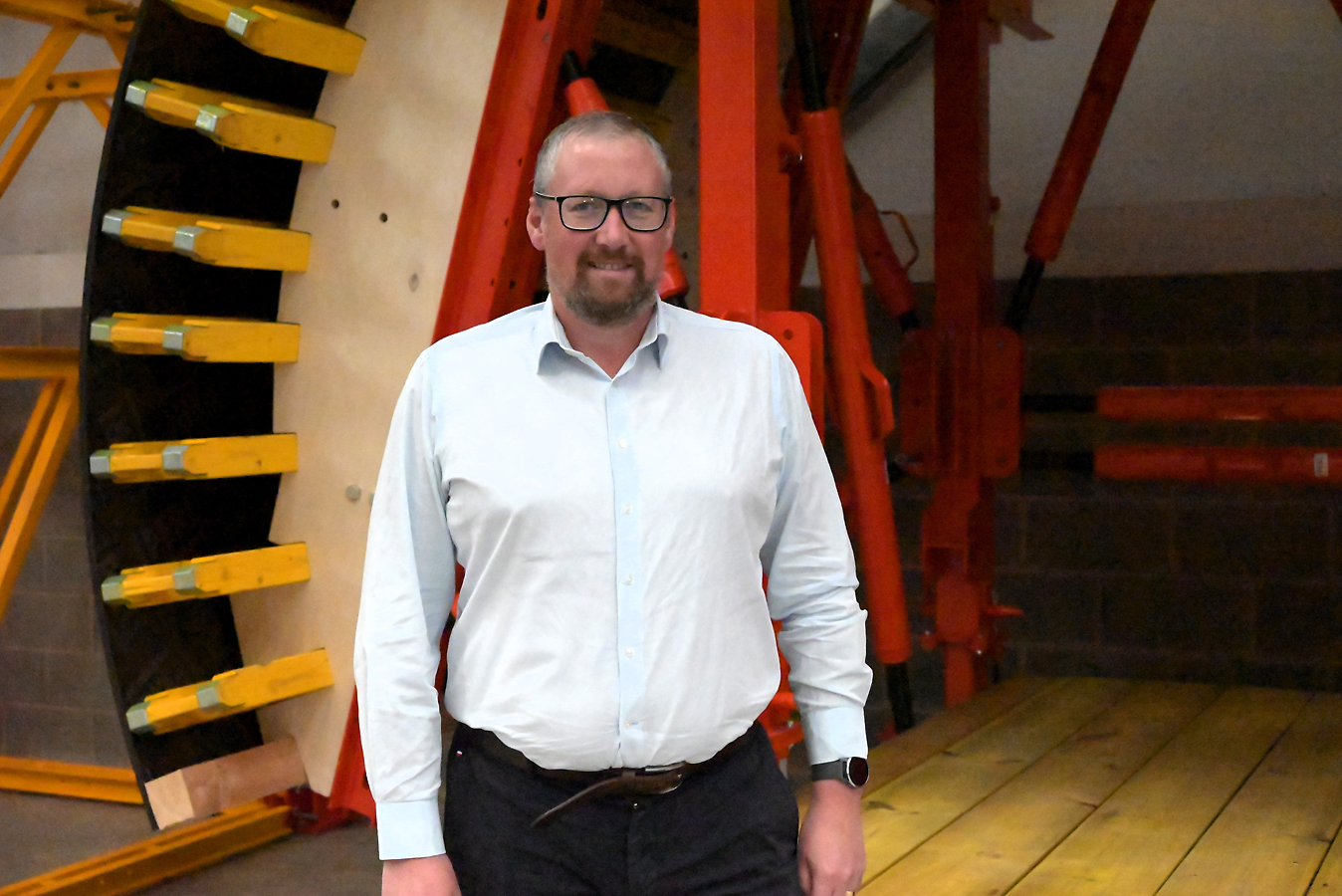
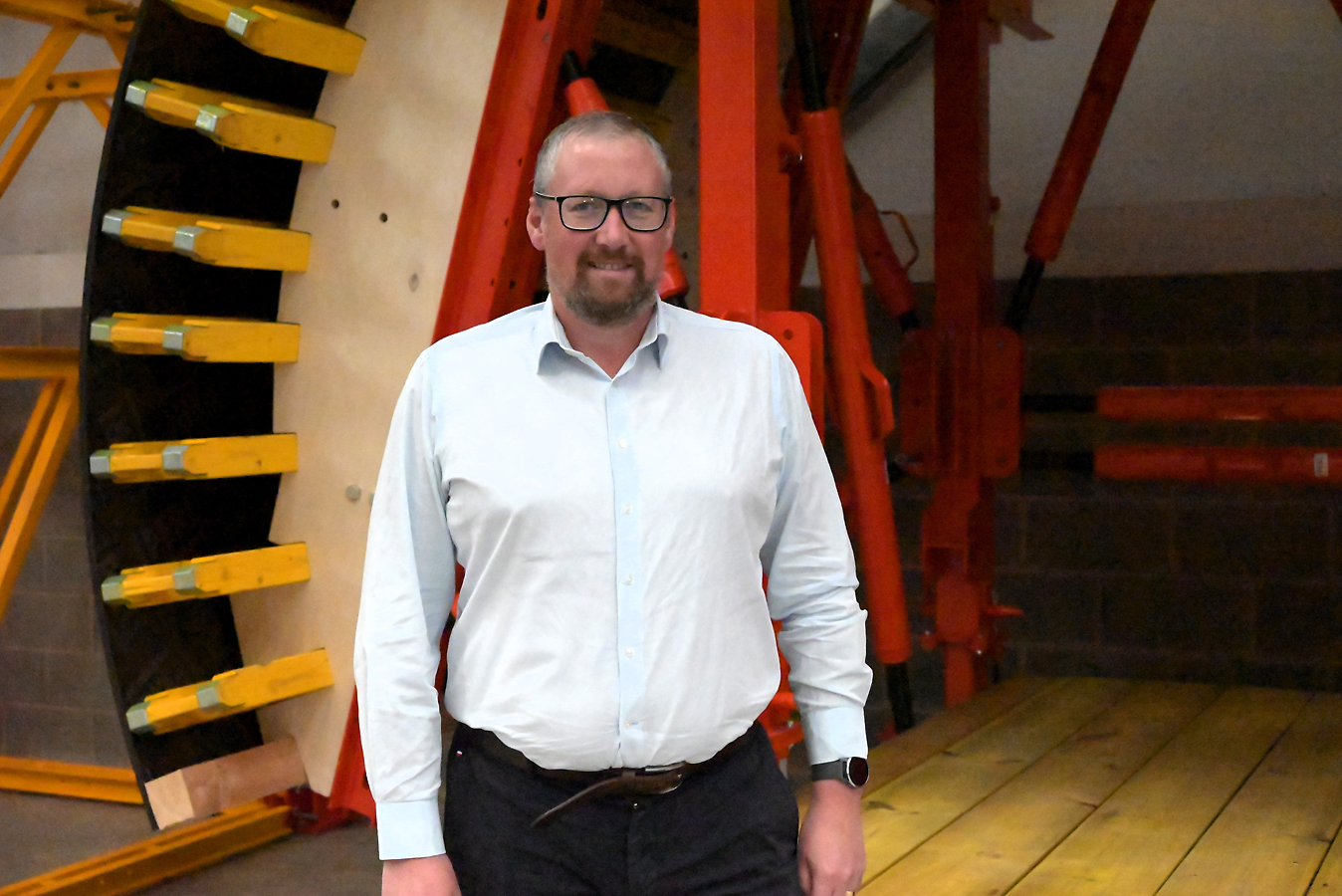
Efficiencies
Working with a single supplier for a range of requirements can offer significant benefits, especially when compared to the time taken to raise orders with multiple suppliers. This approach can often simplify an already complex end-to-end process for joint ventures and enables better integration between systems.
Customer portals like myPERI are ideal for large-scale projects like power plants, as they enable sub-contractors to manage stock levels and provide visibility of every PERI product on site. All project-related data is accessible on one platform.
We have supplied a range of systems to the HPC site, all of which can work hand in hand with each other using standard components. By blending off-the-shelf components, we can introduce new built-for-purpose systems like our PERI UP or VARIOKIT Traveller to overcome challenges on site.
The integration of our formwork and scaffolding systems is not only more cost-effective than purchasing individual systems from multiple suppliers, but it can also provide a safer and seamless working environment. This is especially important when considering access in tunnels, bridges, or inside a shaft.
Even on a 175-hectare site like Hinkley Point C, it’s vital to conserve space to ensure worker safety and transport material in and out of the site with ease. Off-site fabrication can support these types of challenges as formwork can be assembled, stored and delivered just in time for installation on site.
For the reactor on HPC, we fabricated single-sided climbing (SCS) platforms and 11.4m-high formwork shutters for lift cores elsewhere on site. These types of solutions are difficult to build on site without the space, machinery and skilled labour resources.
Tried, tested and improved
Our team alone created over 2000 designs for HPC, which can be adapted for Sizewell C. Applying the lessons learnt on HPC will guide the supply chain on how to construct Sizewell efficiently.
We’ve continued to evolve in other areas of the infrastructure sector from HS2 to Thames Tideway Tunnel. On Tideway, our engineers developed the climbing formwork solution we supplied previously at the Blackfriars site to accommodate the larger diameter of the shaft at Kirtling Street. This involved enhancing the hybrid RCS (rail-guided climbing) and SCS (single-sided climbing) climbing system with RCS MAX hydraulics, enabling simultaneous climbing of all platforms and faster cycle times.
Working on multiple sites means that we can refine our solutions and apply learnings on complex infrastructure construction.
Right skills and futureproofing
From engineers to on-site operatives, growing skills and nurturing talent across all fields is vital to the success of Sizewell C. This is where educating our workforce through Continual Professional Development (CPD) days and training courses can prove extremely valuable. We can significantly reduce rework and improve the rate at which we get things right the first time with proper training, in both formwork and scaffolding.
For Hinkley Point C, we delivered scaffolding training to over 100 workers including apprentices from local colleges. Partnerships like this enable recruits and contractors to establish a relationship from the outset, whereby the industry’s next generation of construction workers are up to speed with industry standards and best practices.
Minimising the impact of construction
The application of sensor technology on sites like HPC can significantly reduce construction time and give us more clarity about the building materials used on site. This means we have greater opportunities to construct cleaner and greener, whether that’s pouring concrete efficiently or minimising rework.
Our InSite Pressure Sensor was used on the HOR building on Hinkley Point C to understand concrete behaviour under site conditions, the formwork utilisation and the opportunity for optimisation when pouring 9m-high walls.
The real-time data from the pressure sensors were encouraging and presented the team with the information required to optimise the pour rate and maximise shutter utilisation for subsequent pours. Depending on the level of formwork optimisation, it was possible to achieve savings of up to 30%*. This would enable the team to save 3 hours per pour, reducing the pour time from 10.5 hours to 7.4 hours.
Likewise, digital animations are increasingly aiding the planning process. Our Digital Engineering team created an animation for Hinkley Point C’s Adit tunnel to demonstrate the cycling process of our travelling formwork solution. The animation also supported the customer in the implementation phase, where it was used for method statements and as a training resource to show the workforce how it operates.